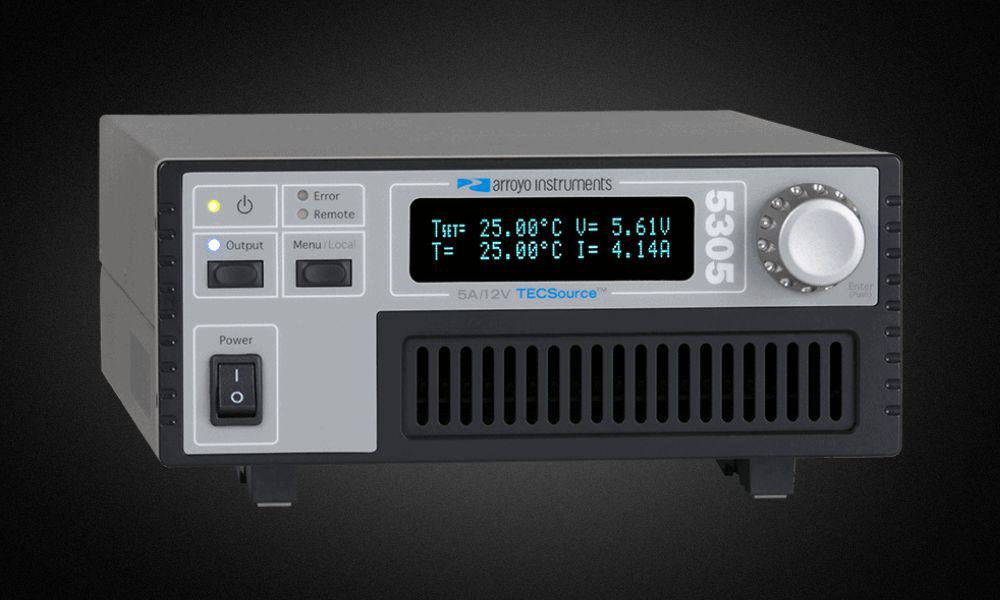
Whether you’re working in the science or engineering field, you’re likely no stranger to using lasers in different projects. These tools are multifaceted, and you can use them to accomplish a lot. However, you need supporting equipment, such as temperature controllers, to ensure your lasers work accurately and remain stable for long periods. Temperature controllers can use different design approaches for controlling temperature. Continue reading to learn about bipolar H-bridge, and direct current versus pulse width modulation control, and the trade-offs of using one design over the other.
Bipolar H-Bridge
A temperature controller must have many internal components to maintain the temperature of your laser or thermal system. It must have temperature sensors to detect when temperatures change, but it also needs a way to control those changes; that’s where the bipolar H-bridge comes in. In Peltier (or thermoelectric cooler)-based systems, the temperature controller must support two current polarities—one to cool and one to heat—and the bipolar H-bridge makes that possible.
The H-bridge acts as a switch, swapping the positive and negative outputs as needed to create either a positive or negative current for the TEC. The benefit of this design is that a single internal power supply can be used to produce both positive and negative currents. Care must be taken in handling the zero-crossing—switching—of the output so that there are no glitches that prevent stable operation around zero. Both direct current and pulse width modulation designs use H-bridge outputs.
Direct Current
Direct current is using a steady flow of current to the output, where the current is adjusted up or down as needed to maintain the target temperature, and only the necessary voltage for that current is output to the TEC module. Because the internal power supply may generate a higher voltage than is necessary for the TEC module, that “excess” voltage is turned into heat inside the unit, lowering the wall-plug efficiency of the temperature controller and expelling waste heat into the room.
Pulse Width Modulation
By comparison to direct current operation, pulse width modulation operates at the full current and voltage of the TEC module, but only for short periods of time. “Pulse width modulation” means the current is turned on and off rapidly, with the difference between the “on” and the “off” periods varied to change the average current of the system. The frequency of the changes is typically hundreds or thousands of times per second, well above the time constant of most thermal systems so that the TEC module behaves similarly to the equivalent average power that might be produced with a direct current design.
Design Tradeoffs
Generally, pulsed width modulation systems are more efficient, produce less waste heat, are lighter and more compact.
With so many benefits, why consider a direct current design?
Noise.
Pulse width modulated designs are electrically noisy due to the high-speed changes of current. This electrical noise has many frequency components and effectively shielding the rest of the system from this radiated electrical noise is difficult, if not impossible. For sensitive applications, such as those using lasers, the noise will translate directly into the optical signal being produced by the laser, and on into the rest of the system. Direct current designs also generally have higher accuracies as compared to their pulse width modulated counterparts.
If your application and device are not sensitive to noise, a temperature controller using a pulse width modulation design may be an acceptable solution, but for the best performance and lowest noise, particularly in laser applications, a direct current design is the best choice.
Here at Arroyo Instruments, we only use direct current designs in our temperature controllers (TEC), so you are guaranteed a system that provides the best possible performance for your laser and thermal applications.